Model A Pump Station in HEC-RAS, HydroCAD, XPSWMM, and HEC-HMS
A storm water pump station (Figure 1) is needed in low areas of a drainage system where drainage by gravity is not possible, such as a depressed roadway segment. Pump station design is a complicated task which requires engineers from different disciplines to work together including structural, hydrologic and hydraulic, electrical, mechanical, civil, and architecture. FHWA has several publications dedicated to pump station design such as HEC-22 and HEC-24.
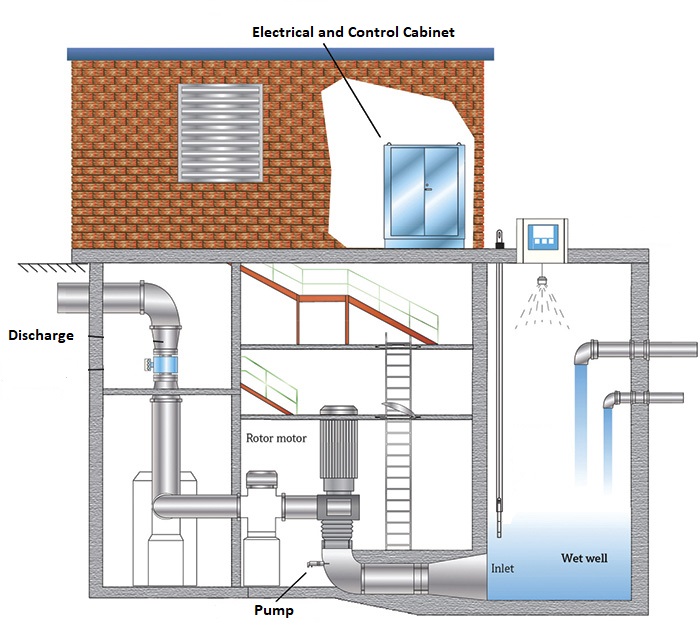
From conservation of energy perspective, a pump station is to lift water from a lower elevation to a higher elevation (the difference between the two elevations is the static head H-static, independent of pump flow rate) by electrical and mechanical energies. During pumping, some electrical and mechanical energies are converted to heat energy when overcoming various frictions throughout the drainage system Hf, which a function of pump flow rate. If the velocity head difference is insignificant, the required total dynamic head (TDH) is expressed as H-total = H-static + Hf. A pump will operate at the point where the system head loss curve intersects the pump curve (Figure 2).
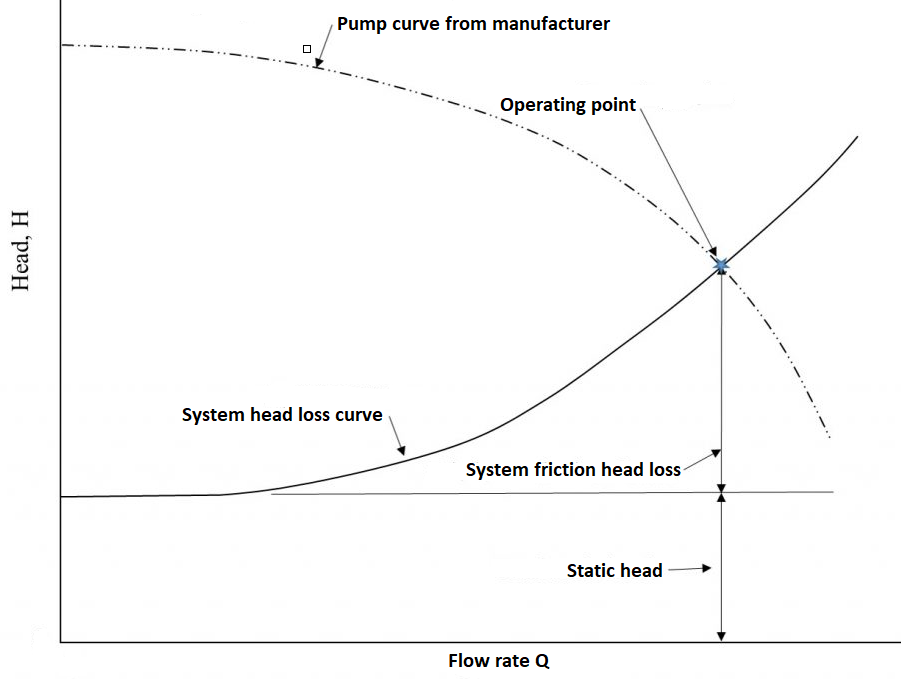
A force main is a pressurized pipe that conveys sanitary sewer or storm water under pressure from the discharge side of pump stations. Most of the time, the force main is not modeled explicitly and its friction loss is to be incorporated into the pump curve by subtracting its values from TDH (Figure 3). For HEC-RAS and XPSWMM, this means the pump curve revision process needs to be done outside the programs. HydroCAD and HEC-HMS give a modeler two options:
- Provide a revised pump curve as input after subtracting system friction loss externally and the friction loss or equipment loss is be entered as zero;
- Apply the original pump curve. For HydroCAD, supply the discharge pipe length, size and Hazen-Williams coefficient to let the program calculate the system friction loss and subtract it from the original pump curve automatically. For HEC-HMS, enter a fixed friction loss/equipment loss which is independent of pump flow rates.
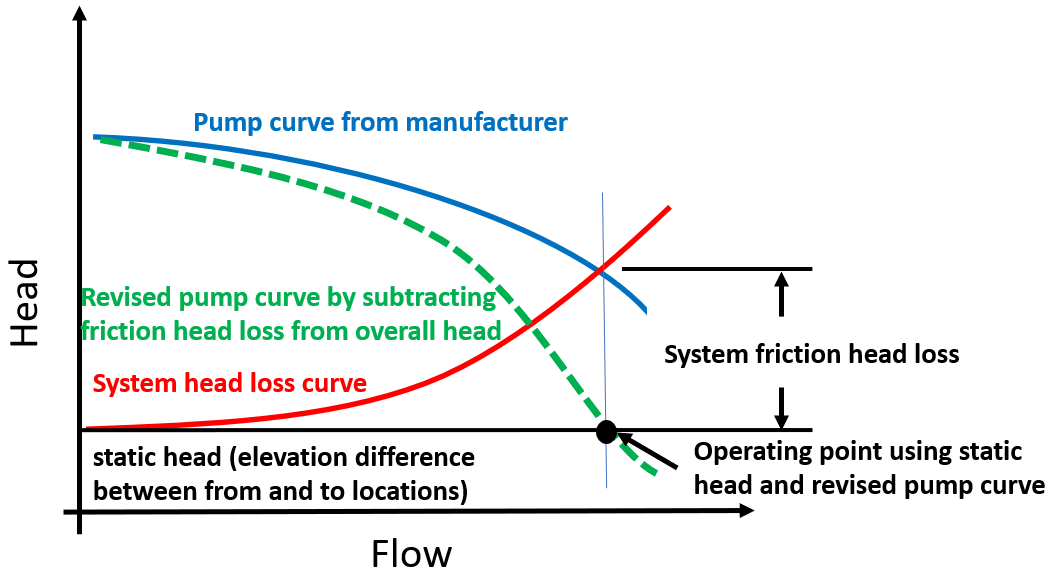
A simple pump station is established in HydroCAD, HEC-RAS and XPSWMM to examine their modeling capability (Figure 4). In this example, the force main is not modeled explicitly (except the HydroCAD model) and its impact is incorporated into the revised pump curve.
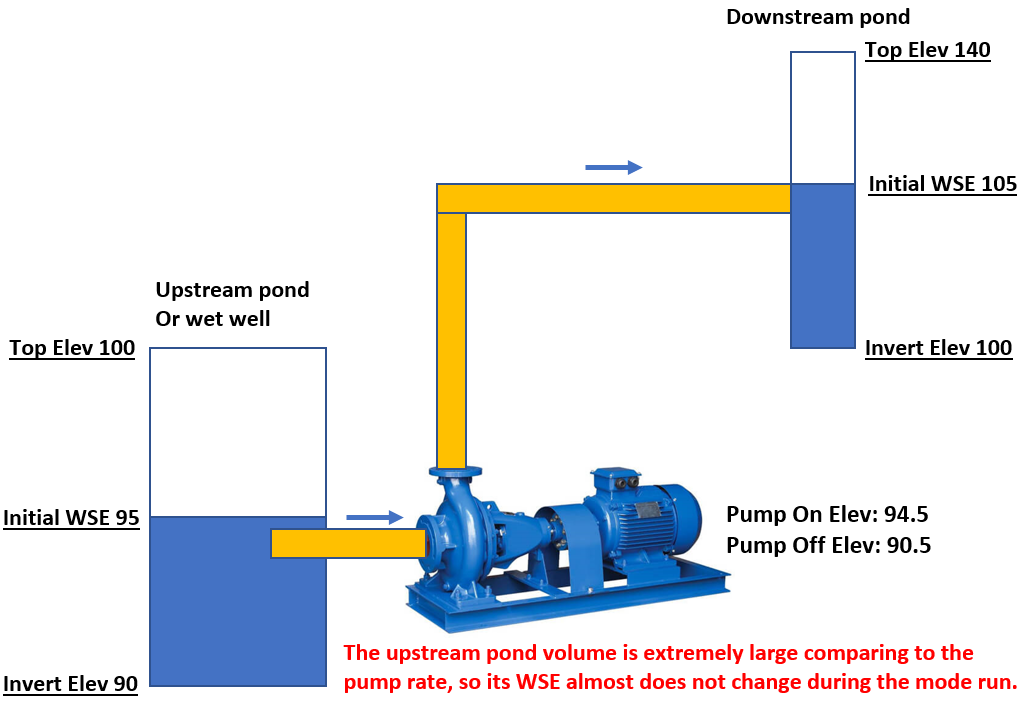
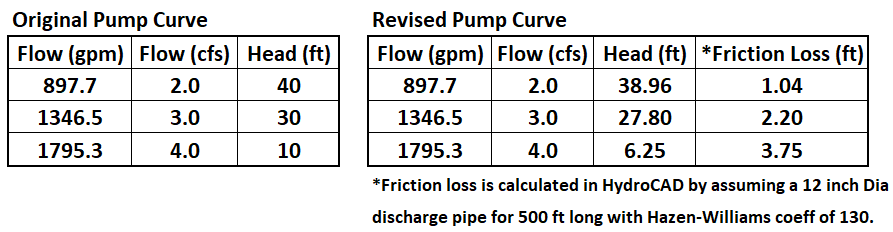
- Pump Station in HydroCAD
To model the pump station in Figure 4, create a new HydrocAD project file and make sure the pond routing method is “Dyn-Stor-Ind” so the tailwater in the downstream pond can be “felt” by the pump.
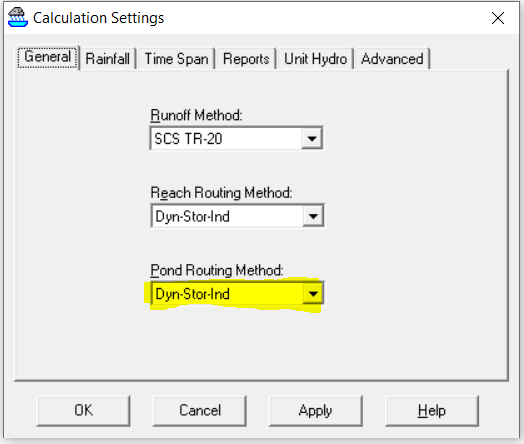
Add two ponds with the bottom sizes of 900′ x 1800′ and 200′ x 200′ respectively. The upstream pond has the pump as an outlet (Figure 6). In this example, the original pump curve is provided and the friction loss is calculated by HydroCAD based on the discharge pipe data provided. It is important to enter the pond initial WSE under the “Advanced” tab (Figure 7).
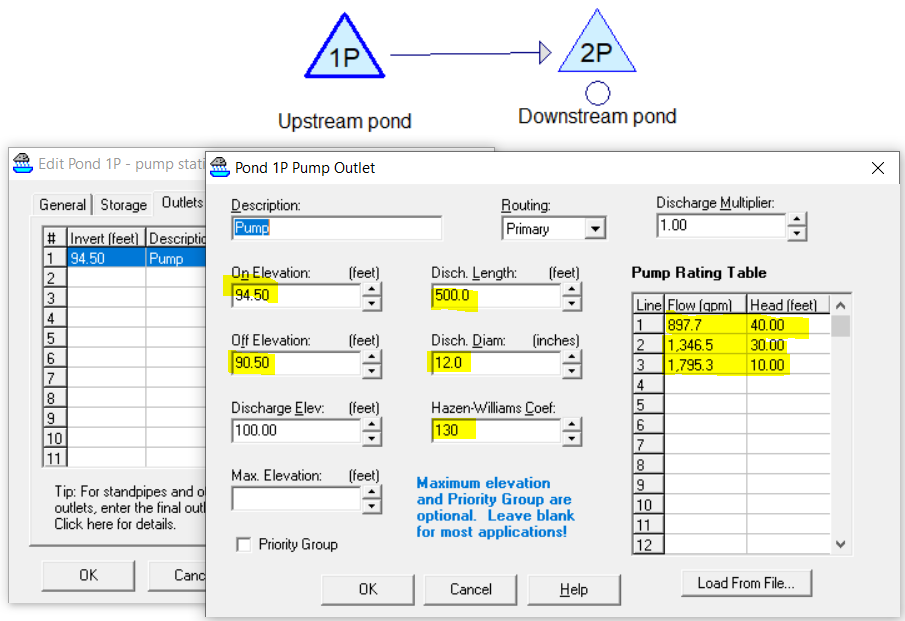
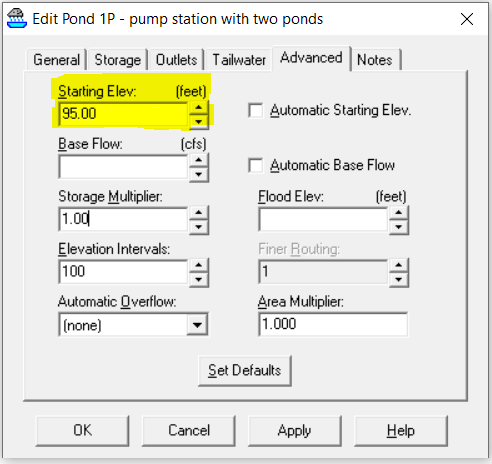
The 48-hr model run results are shown in Figure 8 (upstream pond) and Figure 9 (downstream pond): the pump flow rate is decreased from 3.83cfs@0.0hr to 3.12cfs@48hr while the downstream pond stage rises from Elev 105.00′ to Elev 119.94′ during the same time period.
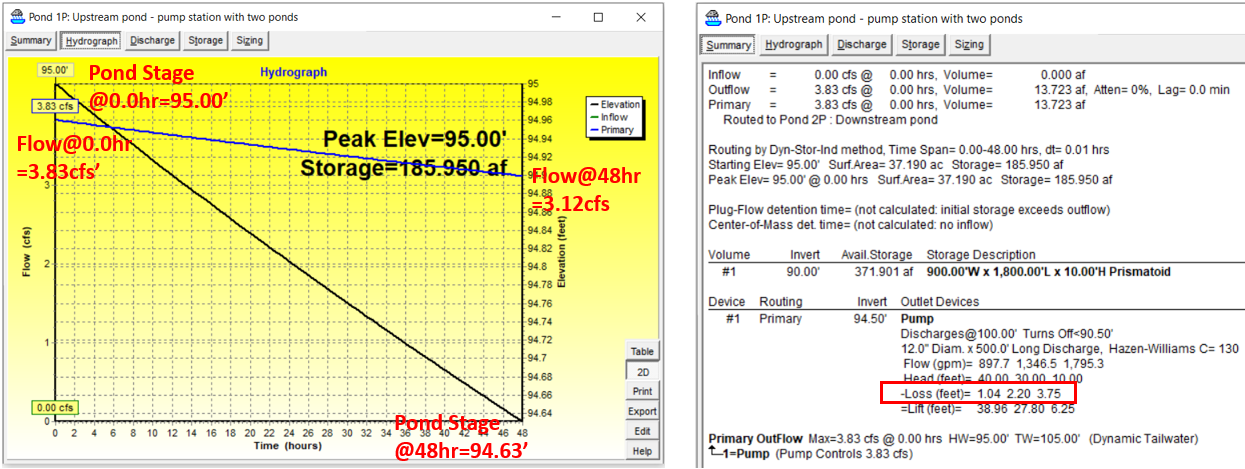
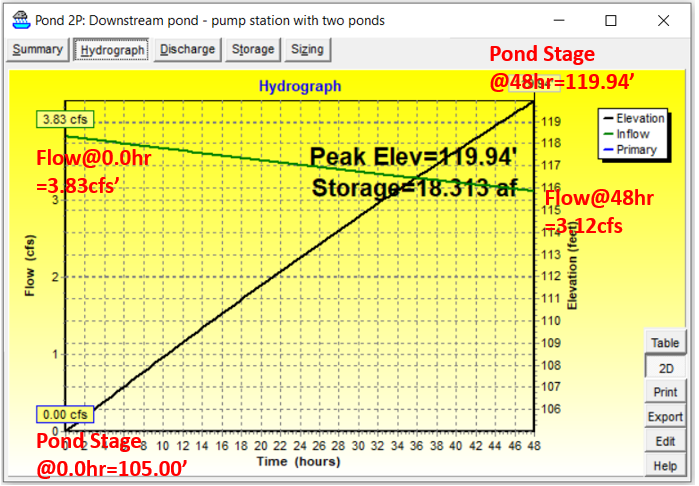
- Pump Station in HEC-RAS
A HEC-RAS unsteady state model is established to model the pump station in Figure 4, which consists of two ponds (storage areas, Figure 10 & Figure 11) and a pump station (Figure 12). In Figure 12, the pump curve is the revised one after the friction loss being taken away.
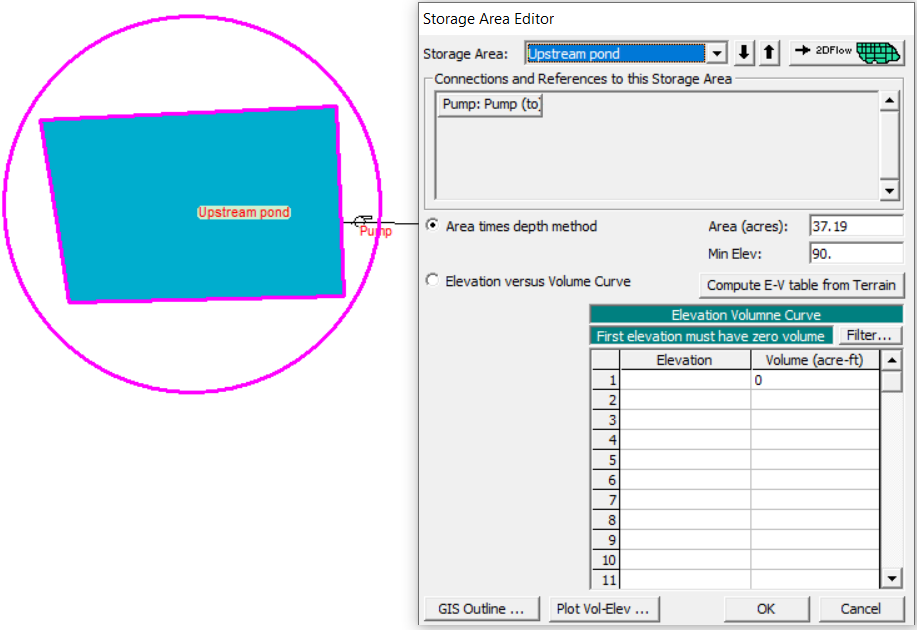
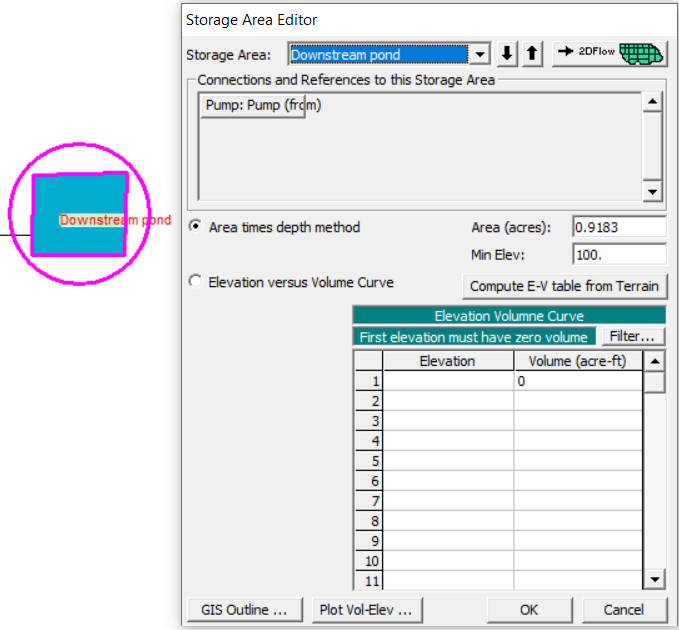
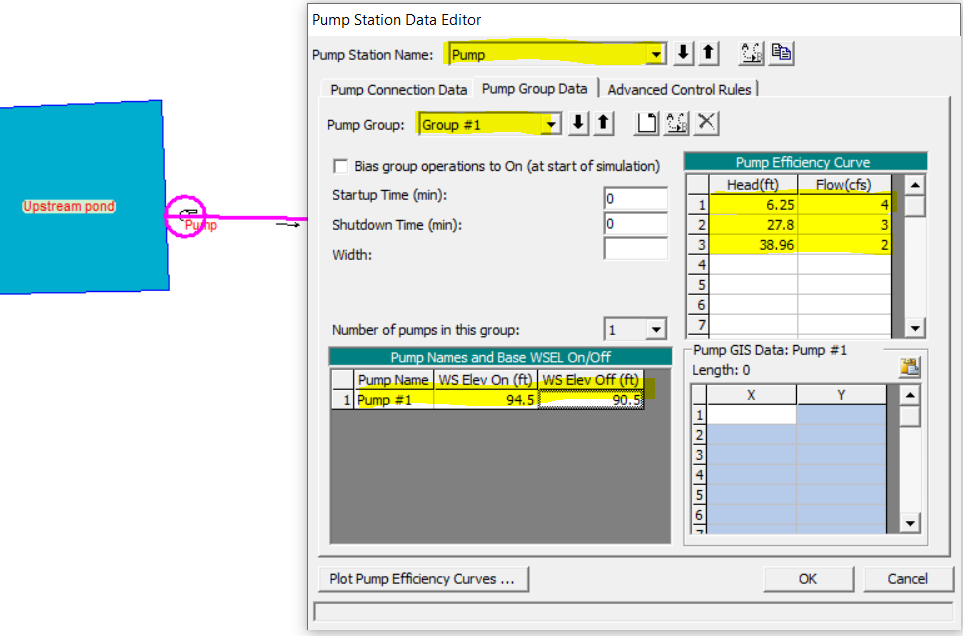
After specifying the initial WSE of the two ponds (Figure 13), run the model for 48hrs. The results of this HEC-RAS model match those of the HydroCAD model pretty well as indicated in Figure 14 in terms of pump flow rates and pond stages.
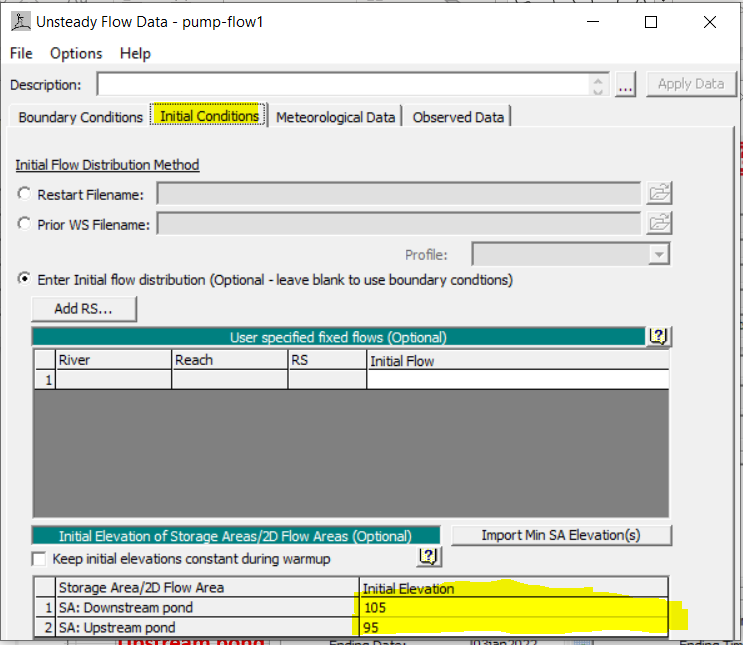
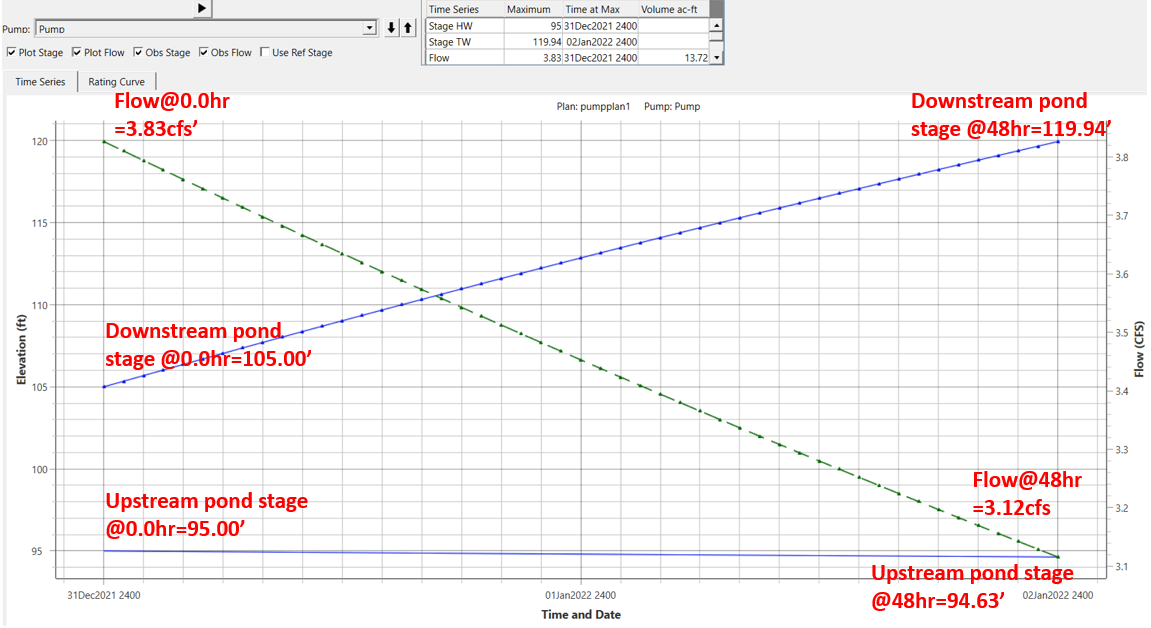
- Pump Station in XPSWMM
Similarly, a XPSWMM model in Hydraulics mode is created to model the pump station for comparison (Figure 15 & Figure 16).
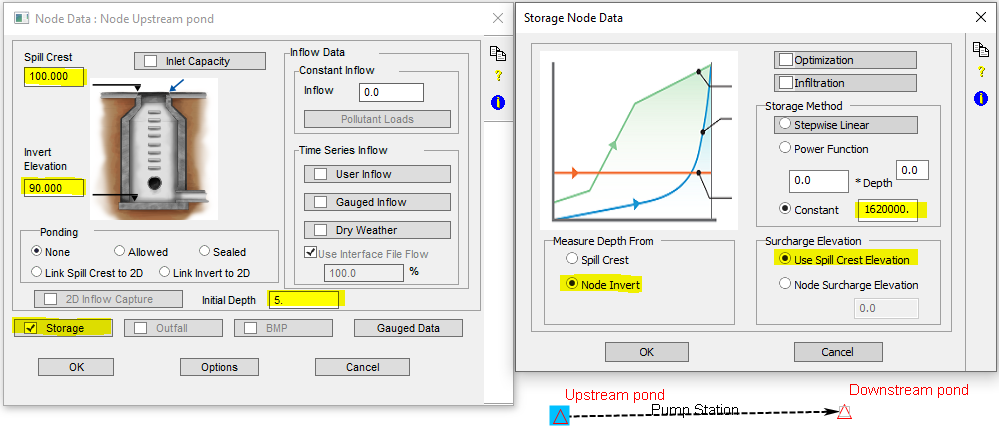
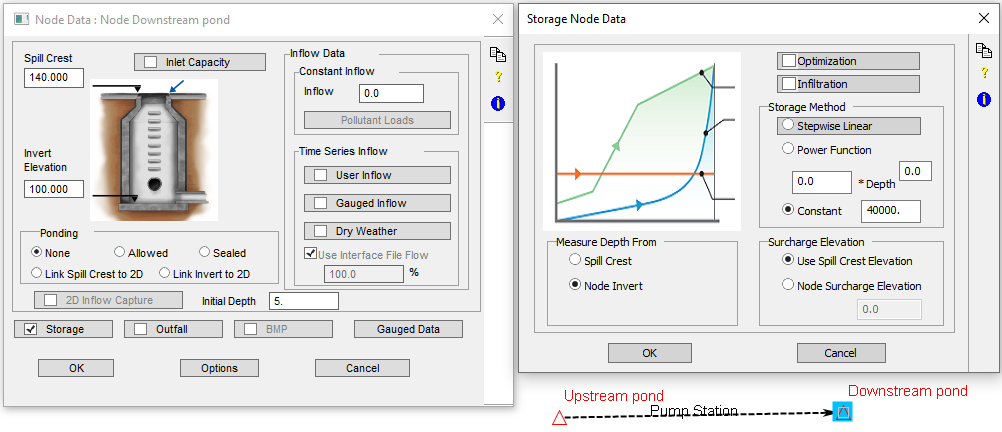
In XPSWMM, a pump station is modeled as a multiple link (Figure 17), and a pump curve must be defined first under Global Data… –> (H) Pump Rating Curves (Figure 18), which is the revised one after the friction loss being taken away.
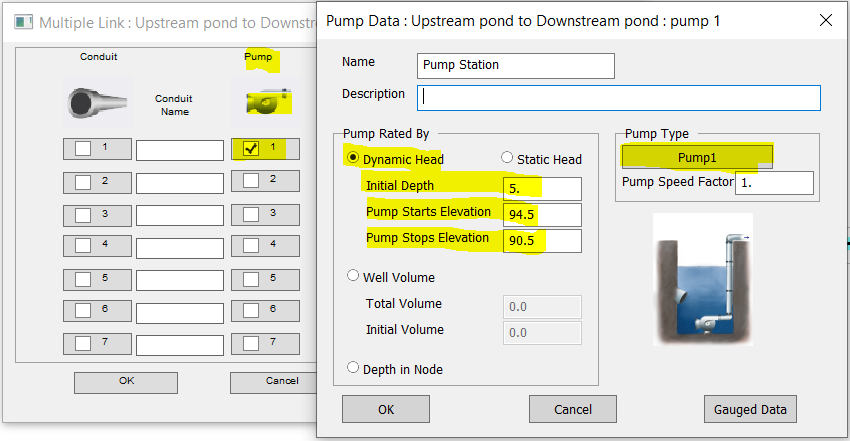
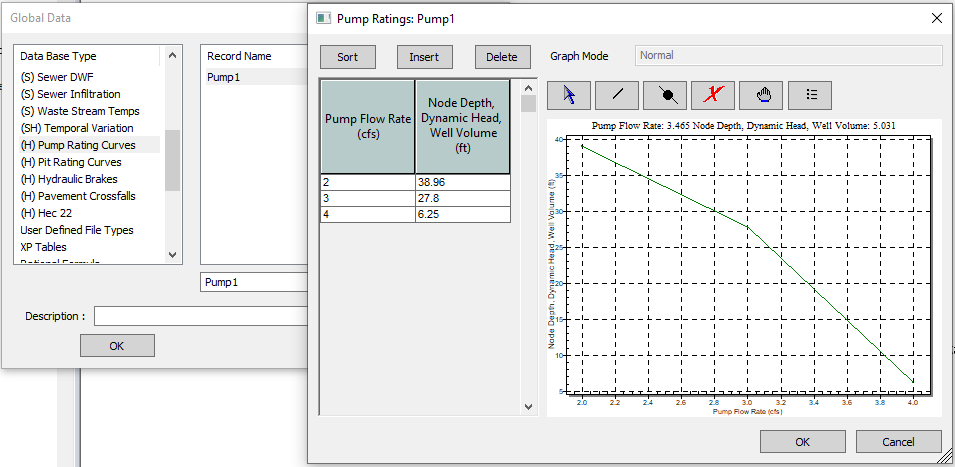
The XPSWMM model established above is run for 48hrs and the results are shown in Figure 19 which are the same as those of the HydroCAD and HEC-RAS models.
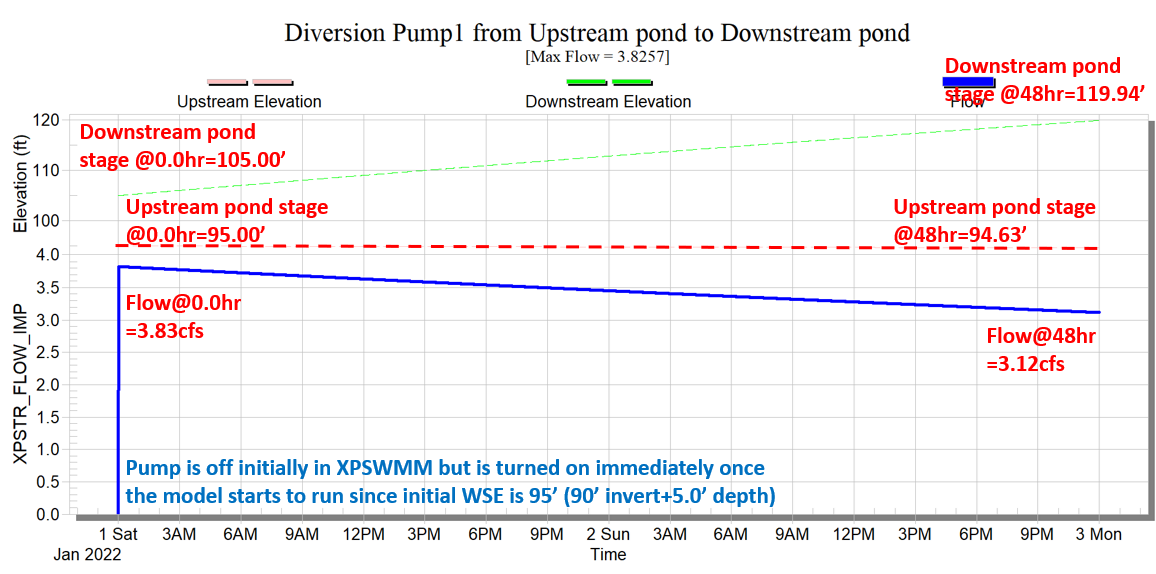
In summary, a pump station rated by dynamic head can be modeled by HydroCAD, HEC-RAS, or XPSWMM; for this very simple example pump station, the three programs are able to generate exactly the same results.
If a discharge pipe is raised to pass over a levee system, the static head should be calculated from the highest elevation in the pump line as indicated in Figure 20 (HEC-RAS) and Figure 21 (HydroCAD). As a result, the pump flow rate is smaller (Figure 22) due to the higher required static head.
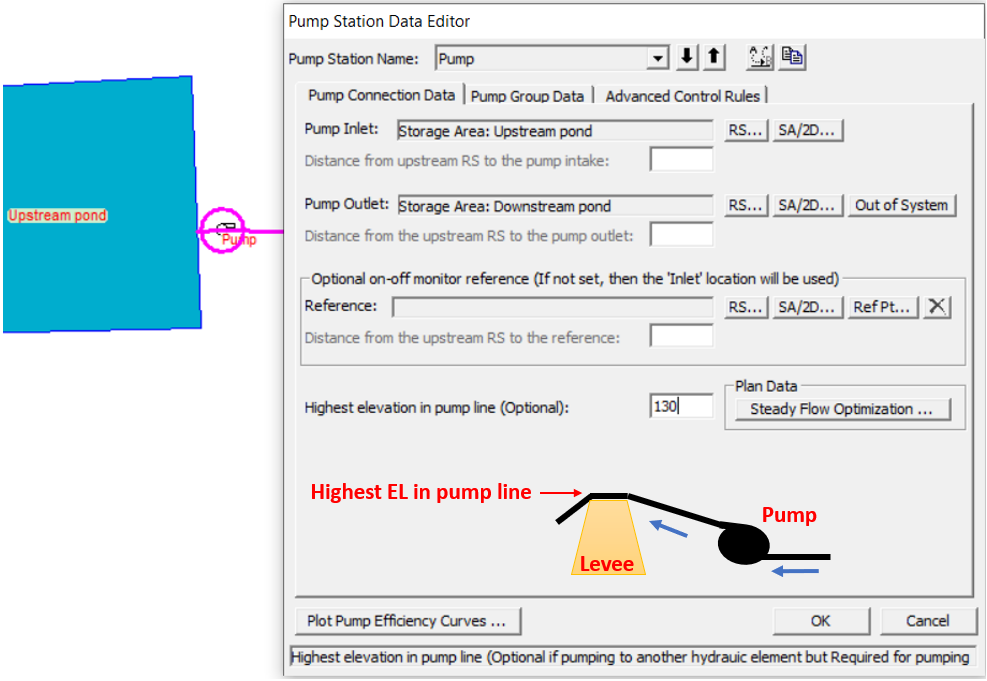
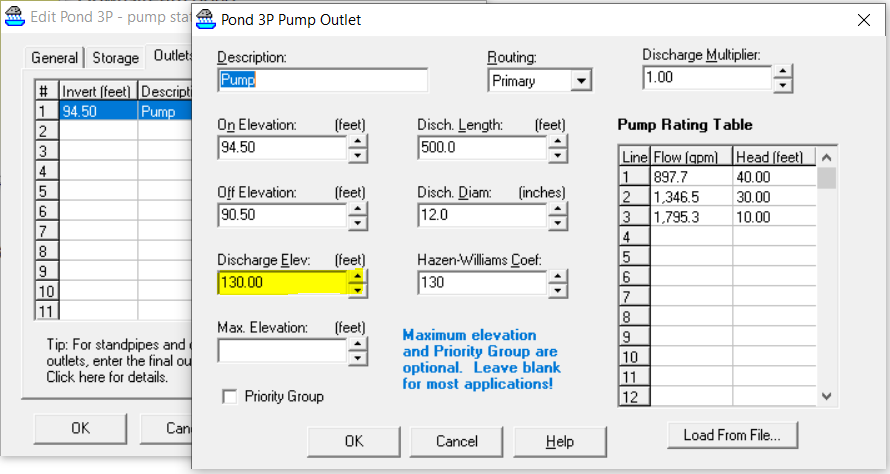
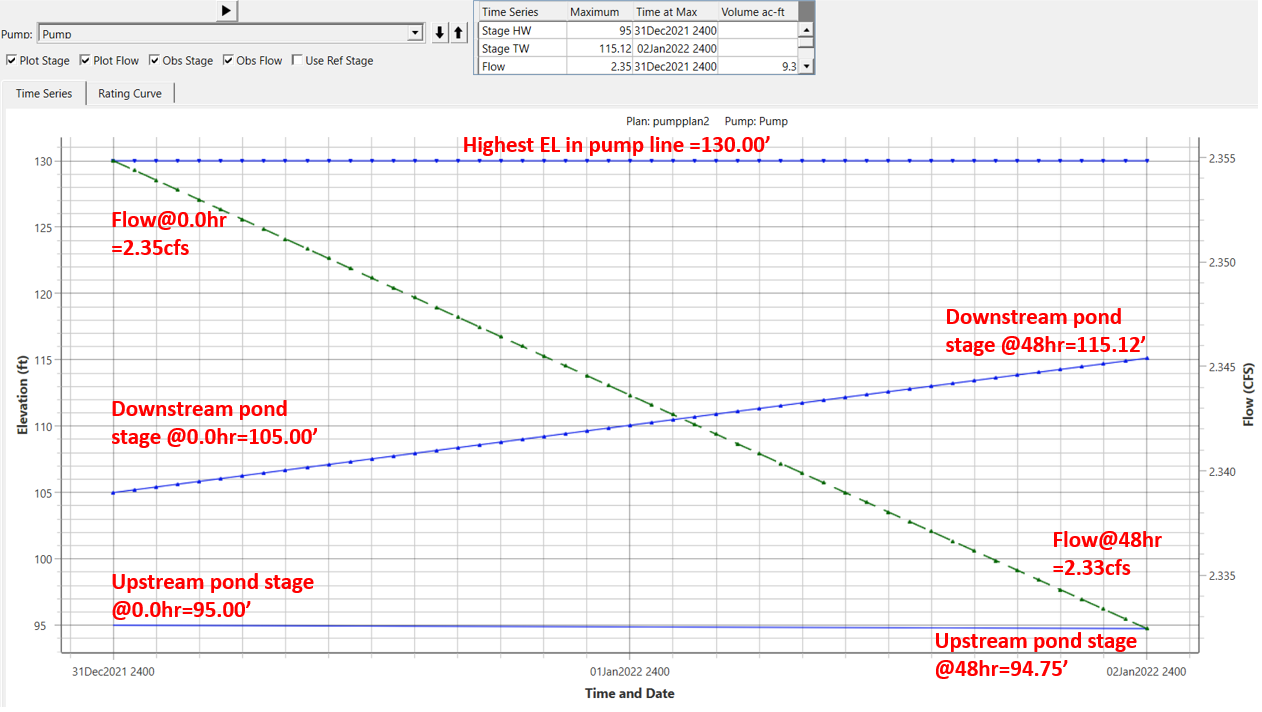
- Pump Station in HEC-HMS
A pump station can be modeled in HEC-HMS as an outflow structure of a reservoir (Figure 23 and Figure 24).
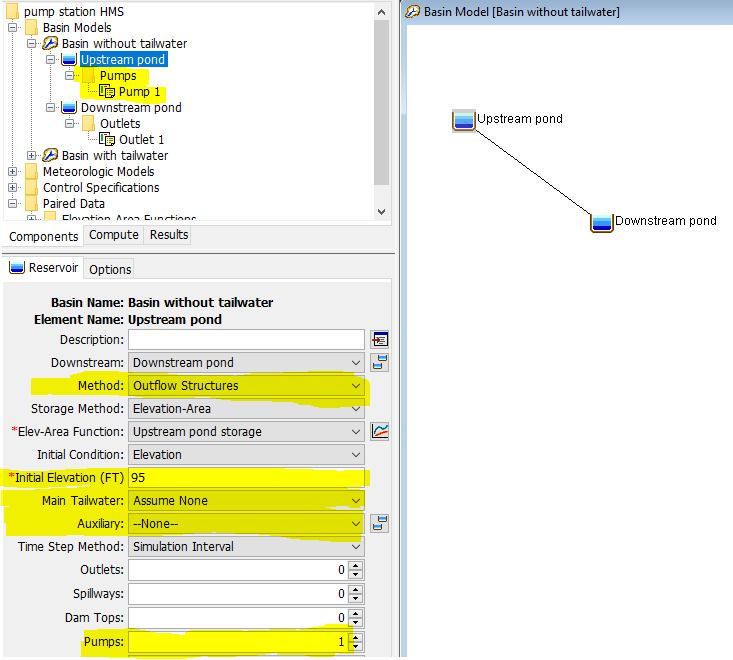
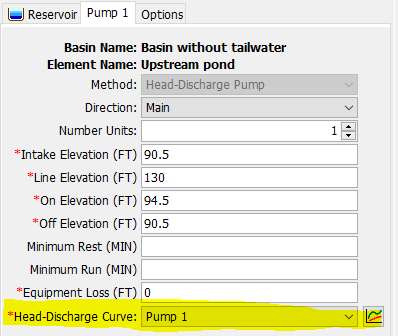
The pump curve is provided as an Elevation-Discharge paired data in HEC-HMS (Figure 25). Supply the original manufacturer’s pump curve if a fixed friction loss is entered separately as Equipment Loss (FT); otherwise, enter the revised pump curve by subtracting friction losses externally as explained above.

As illustrated in Figure 26, usually Line Elevation > On Elevation > Off Elevation > Intake Elevation in a pump setting.
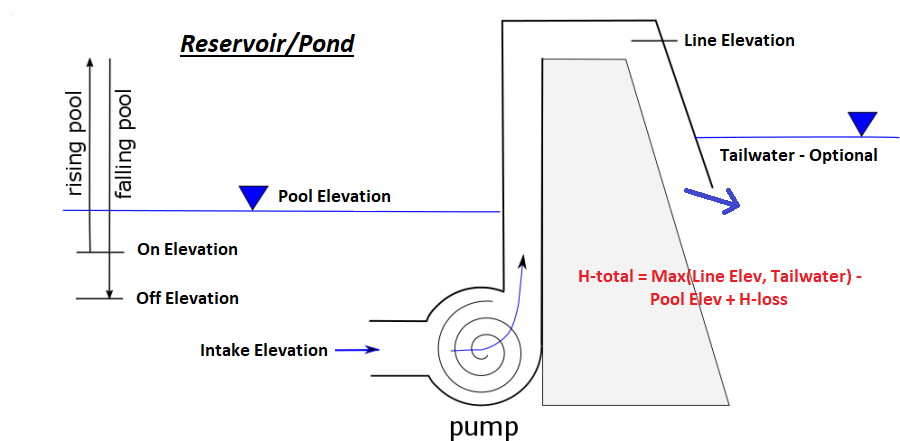
A tailwater condition in the format of an Elevation-Discharge rating curve can be assigned to the reservoir (Figure 27). Under this scenario, the required dynamic head H-total is to be calculated using the higher value of line elevation and tailwater.
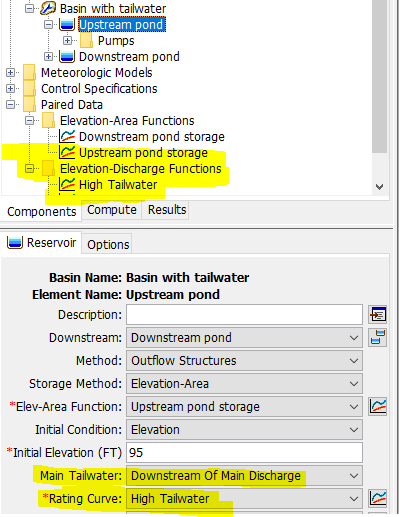
It should be noted that it is not convenient or even possible sometimes to adequately define a tailwater condition in HEC-HMS. A modeler shall consider using other modeling tools introduced above if the tailwater condition is critical to properly model a pump station.
The above example models of HydroCAD/HEC-RAS/XPSWMM/HEC-HMS can be downloaded here. A HMS example model of pumped detention basin is located here.
Leave a Reply